Ironhead Flywheel Rebuild
Article by Mark Trotta
All pre-2000 Sportsters have taper-shaft flywheels that were designed to be rebuilt. The assembly consists of left and right flywheels, crank pin, sprocket shaft, pinion shaft, male and female connecting rods, roller bearings in cages, and thrust washers.
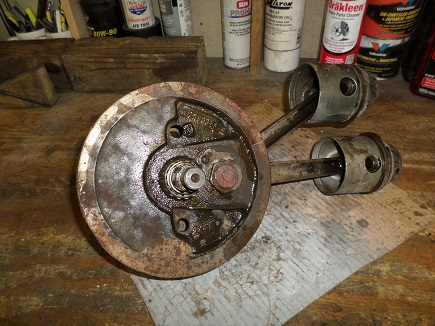
Rebuilding an Ironhead flywheel will include disassembly, cleaning, and inspection of all components. Roller bearings and thrust washers will likely need to be replaced.
***********************
Once the flywheel assembly is out of the cases, check the inner and outer sprocket shaft bearings for wear and excessive play.
Remove Sprocket Shaft Bearing
The inner sprocket shaft bearing is a press fit and you'll need a puller to pull it off the shaft.
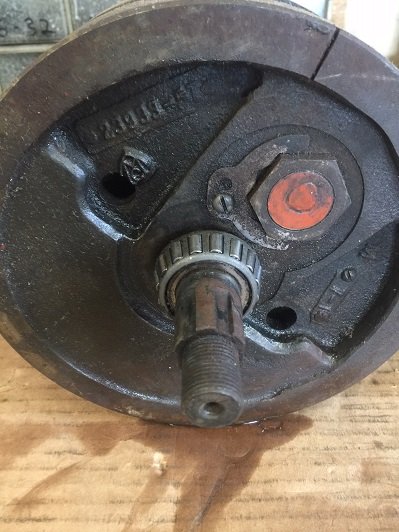
The Harley tool number is 96015-52 which you can buy or make. You can also modify a two-jaw puller to remove it. I fabricated the tool below to remove the inner sprocket shaft bearing.
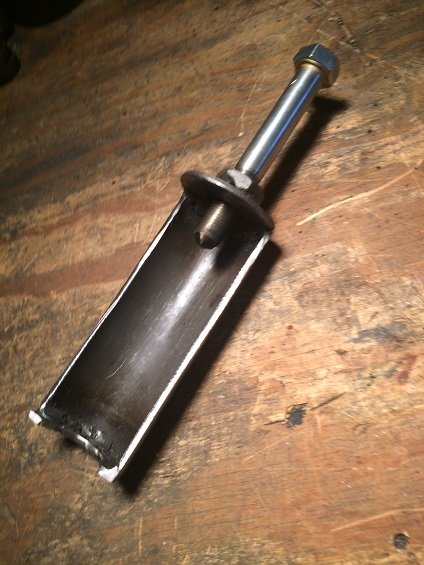
Read: Remove Harley Sprocket Shaft Bearing
***********************
Other Tools Needed
To remove and install the crank pin you will need an 1-5/16" socket or wrench. The sprocket shaft and pinion shaft nuts require an 1-3/16" socket or wrench. You can buy a Harley wrench for these (H-D part number 94546-41), or use impact sockets.
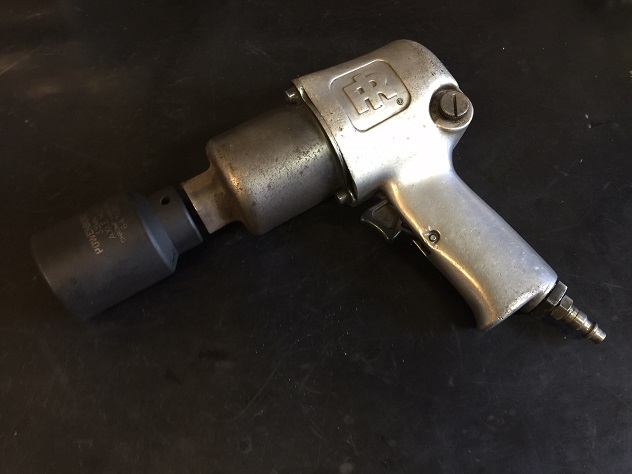
You need to have a way to hold the round flywheels in place while you tighten and loosen the nuts.
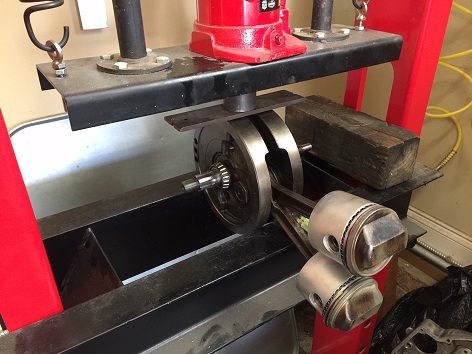
There are several ways to do this, a shop press is easiest.
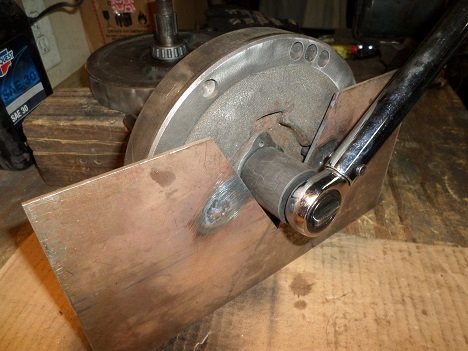
Or, you can buy or make a holding jig.
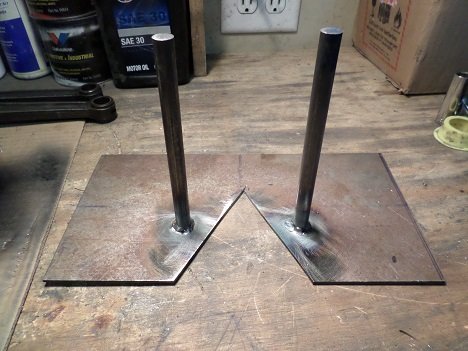
***********************
Crank Pin Nut Lock-Plates
From 1957 through early 1978, Sportster crank pin nuts were fitted with lock-plates and bolts. Thereafter, they were deemed unnecessary by the Motor Company.
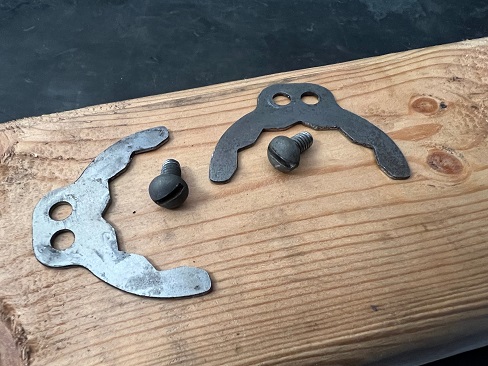
Rule of Thumb: If yours has them, re-use them.
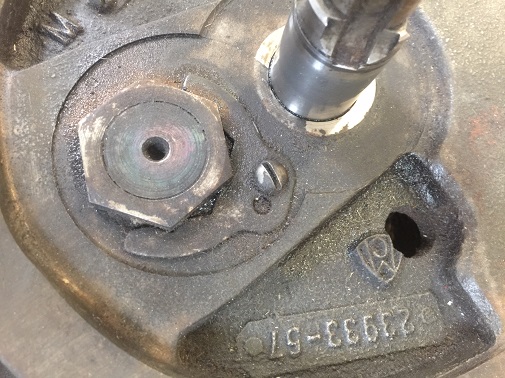
Lock-plate screws are 10-24 x 3/8".
***********************
While removing the connecting rods from the crank pin, be careful of the roller bearings and cages. The bearings are loose and will go all over the place.
Left and Right Flywheels
There is a left and a right flywheel. The one stamped "A" has two keys and has the timing mark on it. The "B" flywheel has one key.
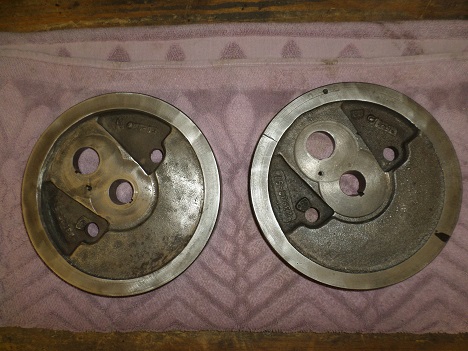
Ironhead flywheels are made from forged steel and extremely durable. I have seen at least four different casting numbers, there may be more.
'Commonized' Flywheels And Shafts
From 1957 through mid-1981, Sportster pinion shafts and sprocket shafts had an end taper of 8 degrees. Beginning in late 1981, these were changed to a 6 degree taper. The female taper in the flywheels was changed as well.
These commonized engine shafts and flywheels were a running change at the factory. Old inventory was used up first, so an early 1982 Sportster could very will have the older style flywheel shafts. Assembly and disassembly is the same for either type of flywheel, but the torque values are different.
***********************
Are Ironhead Flywheels Interchangeable?
Early and late 1000cc flywheels and shafts do not interchange with each other, not only because of the slight angle difference, but because the oil holes of the crank pin are in different positions.
All 900cc sprocket shaft, pinion shaft, and flywheels are interchangeable.
Ironhead Crank Pin
The crank pin is one of the most highly stressed parts in the engine, and they have been known to fail if over-stressed. Carefully examine for wear, grooves, pitting, and out-of-round.
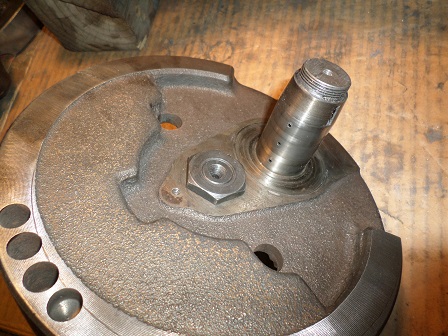
If the surface is worn at all, replace it. This is not a place to cut costs - it will cause a lot damage if it fails!
Crank Pin Replacement
Early Harley-Davidson Sportsters (1957 through mid 1981) used a three-hole crank pin (HD #23960-54). The part number for late 1981 through 1985 models is H-D #23960-80A. Early and late crank pins are similar but do not interchange.
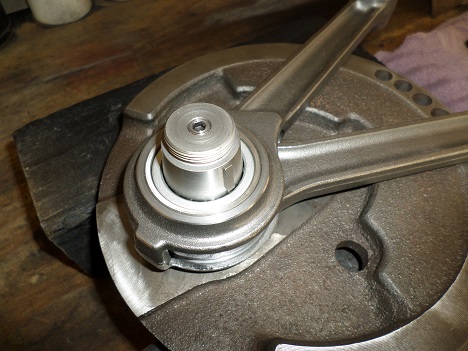
Aftermarket crank pins are offered in standard and oversize O.D. They usually come supplied with new heat-treated nuts as well.
Flywheel Thrust Washers
While checking both flywheels for cracks, examine the flywheel thrust washers carefully. If they are worn or grooved, replace them.
Early Sportster thrust washers were made of steel, later ones were made of bronze. Steel washers should be used with steel roller bearing cages. Bronze washers should be used with aluminum roller bearing cages.
Replacing Thrust Washers
Removing thrust washers usually requires drilling a small hole (1/8" or smaller) slightly deeper than the thickness of the washer at the outer edge of the washer. This will allow you to stick a pointed tool underneath and pry it out. Don't remove more metal than necessary.
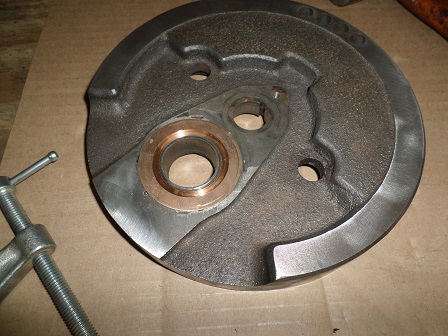
Once you get the washer out, Measure the washer thickness and replace with the same size - they do make oversized washers if needed.
A flush fit is important - Clean the recesses out with a scribe or awl. If the washer does not seat fully, the female connecting rod may not give enough clearance for side play.
Once you have a flush fit, peen the new washers into position at several points. This is an easy process that distorts the metal just enough to hold it in place.
Sprocket Shaft and Pinion Shaft
The sprocket shaft and pinion shaft will most likely be re-usable, but a good engine builder never assumes anything. Check both shafts before assembling. I modified my homemade truing stand and did a quick check on both sprocket shaft and pinion shaft run-out.
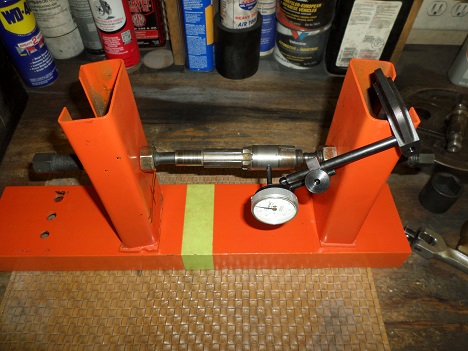
Roller Bearings And Cages
Early Ironheads left the factory with steel roller bearing cages, which Harley-Davidson later updated to aluminum cages. Again, steel thrust washers should be used with steel cages, and bronze thrust washers should be used with aluminum cages.
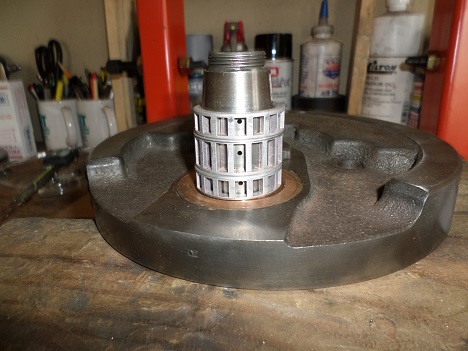
Many builders upgrade to the bronze washers/aluminum cages when rebuilding early engines (yours may have already been updated).
Connecting Rods
If your rods are worn and need replacing, consider buying a complete kit, which includes new rods, cages, and roller bearings. The imported kits made in Japan are a good quality. I've built two motors with them without issues.
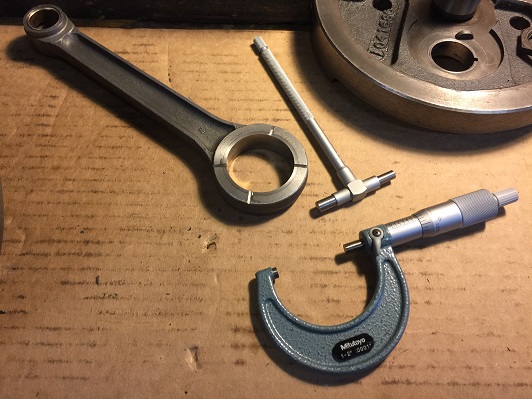
Flywheel Assembly
Although the assembly can only go together one way, re-assembly takes patience and attention to detail.
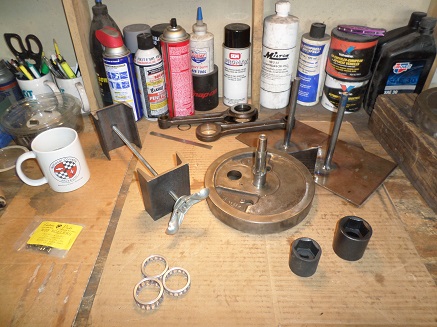
Clean all components thoroughly and dry with compressed air. Blow compressed air into the small oil holes to make sure the oil passages are not clogged.
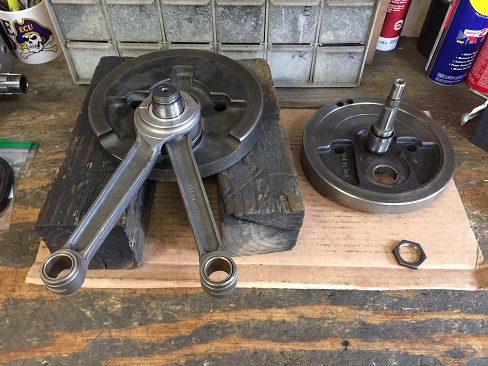
***********************
Flywheel Centering Jig
After the flywheel assembly is back together, it needs to be trued before being put back in the cases. A flywheel centering jig will help get into initial truing.
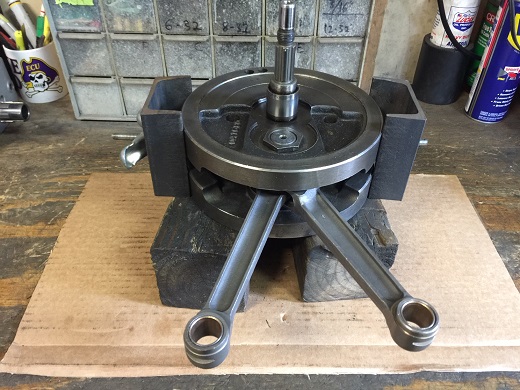
Read: DIY Motorcycle Tools
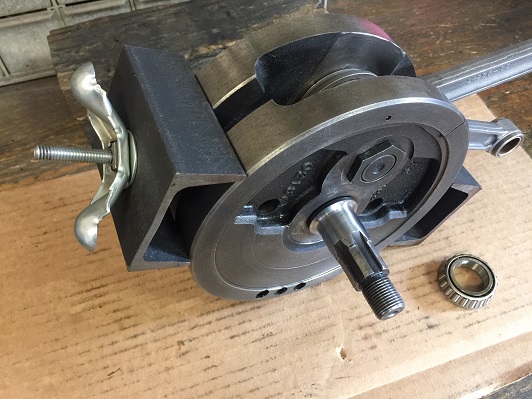
If you haven't already done so, now is the time to press on the inner sprocket shaft bearing. Do this before you start the flywheel truing process.
***********************
Flywheel Truing
For this, you'll need either a lathe or a flywheel truing stand. A truing stand is a nice luxury, but homemade units work just as well. True the flywheel assembly so run-out is within 0.001".
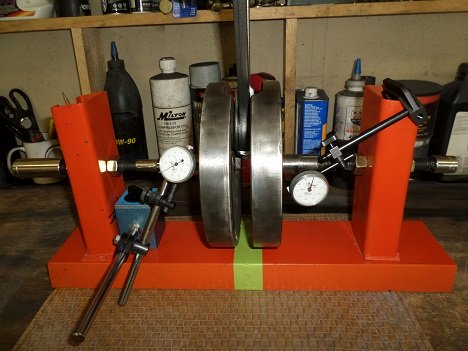
Read: DIY Flywheel Truing Stand
Truing vs Balancing
Truing is about how the two flywheels mate to each other. Balancing is about the actual weight of the flywheels, spoken in terms of grams. Truing is done at the factory, as is balancing, but not to the same degree of precision as would be required for racing.
Flywheel Balancing
Are you doing a stock rebuild with factory parts or a performance upgrade using aftermarket parts? If you're sure you're using original factory parts, the balance is probably OK, but it's a good idea to check that your piston/ring/rod weight isn't way off. If you're re-using original components, your engine should run like it did when it left the factory.
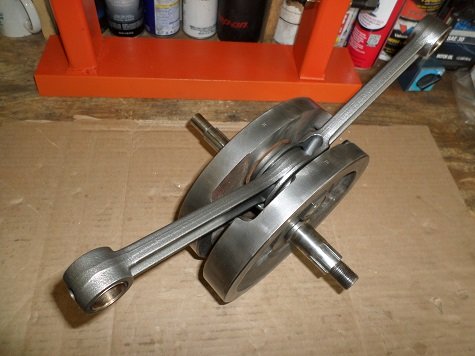
Truing is mandatory, balancing is optional.
Balancing the flywheel assembly components (pistons, rods and other rotating items) will make your engine run smoother and allow higher revs. It is a mandatory step when seeking more horsepower. Balancing can be done either statically or dynamically, and balancing kits are available from S&S for Harley flywheels with tapered crank pins.
***********************
Torque Specs
On 900cc models, sprocket shaft nut gets torqued to 100-110 ft lbs.
On 1000cc models, sprocket shaft nut gets torqued to 100-120 ft lbs.
On 900cc models, crank pin nuts get tightened to 150-175 ft lbs.
On 1000cc models, crank pin nuts get tightened to 150-175 ft lbs.
On 1000cc models with commonized tapers, crank pin nuts get tightened to 150-185 ft lbs.
After 50 ft lbs, tighten the nut in increments, 10 ft/lbs at a time. Double-check your final torque. Be careful not to over-torque, or you may widen the taper to the point where the flywheel must be replaced.
***********************
Notes and Misc
On flywheels with lock plates, when re-installing, never loosen the crank pin nuts to make the lock plates fit. Tighten the nuts a little more until they do line up.
It's always best to check the factory manual for specific year torque specs.
If installing the flywheel assembly into the motor will not be immediate, oil it up and put in a plastic bag. This will keep it protected from dirt and dust.
***********************
Related Articles:
Ironhead Engine Build
Remove Harley Sprocket Shaft Bearing
Best Engine Assembly Lube
Best Digital Caliper For Engine Building
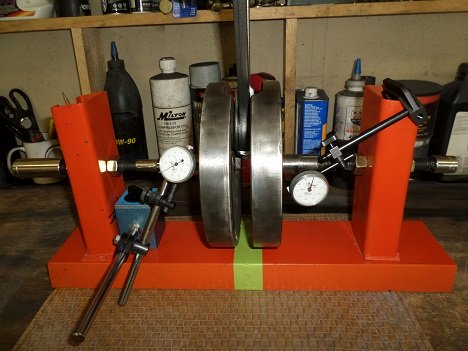